Alloys
Learn about our alloys.
Phosphorus-deoxidized copper with limited High amount of residual Phosphorus, ensuring complete removal of any oxide. Corrosion resistance, excellent welding, soldering and forming properties for a variety of applications such as Plumbing , Heating, Refrigeration, Gas, Medical, HVAC&R and a wide range of Industrial uses.
High Strength low alloyed copper containing a limited amount of Iron. Excellent welding and soldering properties designed specifically for High-pressure Air Conditioning & Refrigeration piping systems and equipment, particularly when CO2 is used as a refrigerant.
Electrolytic Tough-Pitch Copper, commercially pure very high conductivity refined by electrolytic deposition which is then melted and oxidized to the “tough pitch” condition with a controlled low oxygen content. Excellent electrical and thermal conductivity, corrosion resistance and good workability, common uses Busbars, Conductors, Contacts, Terminals and other current carrying applications.
Deoxidized Copper with limited medium amount of residual Phosphorus. High electrical conductivity, corrosion resistance and excellent welding, soldering and forming properties for Electrical and Industrial purposes, common uses Conductors, Terminals, Lugs, Piping.
High Purity Deoxidized Copper with low level residual Phosphorus. Very High electrical and thermal conductivity, corrosion resistance, good welding, soldering and forming properties for Electrical and Industrial purposes, common uses High Frequency Cables, Conductors, Busbars, Terminals, Lugs, Thermostatic Control Tubing.
Free-machining brass contains about 58% copper and 39% zinc. Lead is added to improve machinability, in content of 1-3%wt. The microstructure is constituted by two phases, α and β. Duplex brass is easier to be hot worked by extrusion or stamping and machine. Generally, an increase of Zn content produces stronger alloys with a moderate decrease in corrosion resistance and cold ductility. Other alloys required to be free-machining , yet retaining sufficient ductility for riveting or other cold work, contain less lead and more copper. Halcor can produce Leaded Brass Rods, Flat Bars, Sections and Wires. PropertiesLead isn’t soluble in a copper matrix and for that reason lead is dispersed homogenously in the form of fine globules in the microstructure. Lead acts as a lubricant decreasing the friction coefficient between the tool and the material, creating discontinuities that promote the chip fragmentation, reducing the cutting force and the tool wear rate. Additions of other elements such as manganese, tin, aluminum, iron, silicon and arsenic may be used to improve strength and corrosion resistance. Leaded brass is used for its excellent machinability, good strength and atmospheric corrosion resistance.ApplicationsLeaded brass is used for architectural hardware, general purpose screw machine parts, screws, valves, fittings, bearings and specialty fasteners.Material Designation
European StandardsNumber | European StandardsSymbol | USAUNS | GBBS |
---|---|---|---|
CW600N | CuZn35Pb1 | C33500 / C34000 / C34500 | CZ118 |
CW601N | CuZn35Pb2 | C34200 / C35300 / C38500 | CZ119 |
CW602N | CuZn36Pb2As | C35330 | CZ132 |
CW603N | CuZn36Pb3 | C36000 | CZ124 |
CW604N | CuZn37Pb0,5 | C33500 | – |
CW606N | CuZn37Pb2 | C35300 | CZ121 / CZ119 / CZ131 |
CW607N | CuZn38Pb1 | C35000 / C37000 | – |
CW608N | CuZn38Pb2 | C37700 / C35000 / C35300 | CZ128 |
CW609N | CuZn38Pb4 | – | CZ121 |
CW610N | CuZn39Pb0.5 | C36500 | CZ123/137 |
CW611N | CuZn39Pb1 | C37100 | CZ129 |
CW612N | CuZn39Pb2 | C37700 | CZ120 |
CW613N | CuZn39Pb2Sn | C48500 | – |
CW614N | CuZn39Pb3 | C38500 | CZ121 |
CW615N | Cu39Pb3Sn | – | – |
CW616N | CuZn40Pb1Al | – | – |
CW617N | CuZn40Pb2 | C38010 / C37700 / C38000 | CZ122 |
CW618N | CuZn40Pb2Al | C38000 | – |
CW619N | CuZn40Pb2Sn | – | – |
CW620N | CuZn41Pb1Al | C38000 | – |
CW621N | CuZn42PbAl | – | – |
CW622N | CuZn43Pb1Al | C38000 | – |
CW623N | CuZn43Pb2 | – | CZ130 |
CW624N | CuZn43Pb2Al | – | CZ130 |
CW709R | CuZn32Pb2AsFeSi | – | – |
CW716R | CuZn38Mn1Al | C68600 | – |
Due to the maximum lead content of 0.2%, low lead alloys are fully compliant with the California Health and Safety Code (1953) and with Vermont Act 193 concerning lead in potable water systems but also based on Directive 2002/95/EC (RoHS), DM 174 del 06/04/2004, DIN 50930-6 Norm. Brand name for CW510L alloy is Free Brass ™ 1 and for CW511L is Free Brass ™ 2. These alloys, which are suitable for direct contact drinking water applications, are certified under NSF / ANSI 372 standard and are available across the standard round, hexagonal and square bars size range and are suitable for hot forging or machining. Halcor can produce Low Lead Brass- Free BrassTM Solid, Hollow Rods and Seamless Tubes.PropertiesFree Brass™ 1 is suitable for machining and hot forging applications, exhibiting better machinability than Free Brass ™ 2, which is mainly suitable for forging stock and also exhibits better dezincification resistance due to the addition of As. The characteristics of Free Brass ™ alloys are similar to those of lead-based alloys, which allow machining with slight modifications to the tools and the feed rate . Also, the returns of processing (swarf, chippings) can be recycled even if mixed with traditional lead-based alloys. It is also suitable for products destined for the gas industry, since these alloys exhibit minimal risk of sparking.ApplicationsLow lead brass is suitable for drinking water applications (faucets, valves, fittings, etc), for usage in high temperature conditions, for manufacturing of forged and casting parts and for gas fittings.Material Designation
European StandardsNumber | European StandardsSymbol | USAUNS | GBBS |
---|---|---|---|
CW509L | CuZn40 | C28000 | CZ109 |
CW510L | CuZn42 | C28500 | – |
CW511L | CuZn38As | C27453 | – |
Single phase alpha brass is characterized by maximum cold ductility and can be extensively deformed by rolling, drawing, bending, spinning, deep drawing (for the manufacture of cartridge cases), coining, piercing, cold heading and thread rolling. Tubes for heat exchangers are frequently manufactured from the alpha brass, normally of 70/30 composition but often containing alloying additions which enhance corrosion resistance. Substantial quantities of alpha alloys are also used for the manufacture of fasteners such as wood screws, rivets and zip fasteners. For less demanding fabrications such as spring contacts in a domestic electrical socket, an alloy with a higher zinc content can be used, such as CuZn33, CuZn36 and CuZn37 (common brass). These alloys are not quite as ductile as CuZn30, although other mechanical properties are similar. Halcor can produce lead free brass Solid Rods, Seamless Βrass Tubes, Welded Brass Tubes, Flat Bars, Sections and Wires. Material Designation
European StandardsNumber | European StandardsSymbol | USAUNS | GBBS |
---|---|---|---|
CW505L | CuZn30 | C26000 | CZ106 |
CW506L | CuZn33 | C26000 / C26800 | CZ107 |
CW507L | CuZn36 | C26800 / C26700 / C27200 | CZ107 |
CW508L | CuZn37 | C27000 / C27200 / C27400 | CZ108 |
CW724R | CuZn21Si3P | C69300 | – |
High Tensile brass is copper-zinc alloy which combines with additives to increase the tensile strength over that of the simple binary copper-zinc brass. Halcor can produce High Tensile Brass Solid and Hollow rods.PropertiesThis family of alloys exhibit tensile strength in excess of 700N/mm2, along with enhanced properties of wear and corrosion resistance. The alloys containing aluminium have an attractive, naturally lustrous surface and a protective oxide film for extra corrosion resistance. The silicon-containing alloys with manganese have excellent wear resistance, due to the formation of a very hard intermetallic compound, manganese silicide, in the basic matrix.ΑpplicationsThey are suitable for a wide range of applications and service conditions, ranging from decorative architectural use to wear resistant automobile transmission components and the high strength, high integrity equipment used in mines. EU End of Life Vehicle (ELV) DirectiveThe EU End of Life Vehicle (ELV) Directive, adopted in September 2000, includes provision for phasing out metals such as lead used in automotive components. Applications for these copper alloys include bearing shells and bushes, nozzles, connection parts, fixtures and locks.Material Designation
European StandardsNumber | European StandardsSymbol | USAUNS | GBBS |
---|---|---|---|
CW704R | CuZn23Al6Mn4Fe3Pb | – | – |
CW705R | CuZn25Al5Fe2Mn2Pb | C67000 | CZ116 |
CW708R | CuZn31Si1 | – | – |
CW710R | CuZn35Ni3Mn2AlPb | – | – |
CW713R | CuZn37Mn3Al2PbSi | C67420 | CZ135 |
CW718R | CuZn39Mn1AlPbSi | – | – |
CW720R | CuZn40Mn1Pb1 | – | CZ136 |
CW721R | CuZn40Mn1Pb1AlFeSn | – | CZ114 |
CW722R | CuZn40Mn1Pb1FeSn | – | CZ15 |
CW723R | CuZn40Mn2Fe1 | – | – |
DZR (Dezincification-resistant) brass constitutes the best solution for use in unusually aggressive water supplies. In this environment, conventional duplex brass water fittings can suffer, a form of corrosion known as dezincification. This involves selective leaching of the zinc which can cause fracture of the fitting. Addition of a small amount of phosphorous, arsenic or antimony inhibits the occurrence of the dezincification. Halcor can produce DZR Solid and Hollow Rods and Seamless Tubes.PropertiesBrass at hot stamping or extrusion temperature, contains sufficient β phase to be hot-worked satisfactorily.The B phase can be converted by subsequent heat treatment to an all-alpha structure which is protected against dezincification by incorporating arsenic in the alloy. Forgeable DZR brass, such as CW602N (CZ132), is leaded brass and its machinability is comparable with the leaded duplex brass CW617N (CZ122). They are commonly used for production of water fittings. Rods and bars for machining are heat treated by the materials supplier to put them into the dezincification-resistant condition. Forging stock is supplied without heat treatment since it must be heated after forging to 500-525ºC, held for at least two hours and slowly cooled, to ensure resistance to dezincification. This has to be done by the fittings manufacturer. The need for heat-treatment after forging, to ensure an all-alpha structure, can sometimes be avoided by controlled slow cooling through the temperature range 550ºC to 450ºC. Although, this is a more difficult method to achieve the correct degree of dezincification resistance.ApplicationsThese alloys are used as fittings, stopcocks and valves with a carefully controlled composition, which are made by extrusion or hot stamping. This production process must be followed by heat treatment to ensure that the material will satisfy the requirements of the standard dezincification-resistance test (EN ISO 6509-1). The maximum permitted parameters of dezincification are defined in EN product standards.Material Designation
European StandardsNumber | European StandardsSymbol | USAUNS | GBBS |
---|---|---|---|
CW602N | CuZn36Pb2As | C35330 | CZ132 |
CW511L | CuZn38As | C 27453 | – |
CW625N | CuZn35Pb1.5AlAs | – | – |
CW626N | CuZn33Pb1.5AlAs | – | – |
Naval Brass has a chemical composition of around 60% copper 39% zinc and 1% tin with an amount of lead. These alloys are included in the family of α and β or duplex brass. This category of brass exhibit generally higher mechanical properties than other non-duplex brass. Halcor can produce Naval brass Solid and Hollow rods and Sections.PropertiesAs its name implies, naval brass is widely used for naval and steam-generating equipment and generally for sea water service applications, where a strong, hard material is required. Tin is included in the alloy composition in order to improve the corrosion resistance of the material. Tin tends to inhibit dezincification. Dezincification is a type of dealloying in which one of constitutes of an alloy is removed by corrosion. In this case, Zn is depleted and results in a porous Cu-rich layer. The presence of lead in naval brass assists in the machinability of the metal. This subcategory of brass is named leaded naval brass and contains nominally 60% Cu, 1% Sn, 2% Pb and 37%Zn. These alloys have the equivalent strength and corrosion resistance of naval brass plus considerably improved machinability.ApplicationsNaval brass is used in propeller shafts, marine hardware, decorative fittings, shafting, propeller shafts and turn buckles. There are also many industrial applications, such as welding rods, condenser plates, structural uses, valve stems, balls, heat exchanger tubes, aircraft turnbuckle barrels, dies, and many more.Material Designation
European StandardsNumber | European StandardsSymbol | USAUNS | GBBS |
---|---|---|---|
CW711R | CuZn36Pb2Sn1 | C48400 | CZ134 |
CW712R | CuZn36Sn1Pb | C48200 | CZ112 |
CW714R | CuZn37Pb1Sn1 | C48200 | – |
CW719R | CuZn39Sn1 | C46400 | CZ133 |
HVAC & R
In the HVAC&R sector, our copper and copper alloy extruded products play a critical role in ensuring the efficiency and reliability of heating, refrigeration, and air-conditioning systems.
In air-conditioning systems, the wide range of our products offers the best complete package solution such as our tubes TALOS® ACR INNER GROOVED a critical component of evaporator and condenser heat-exchanger coils, where they facilitate efficient heat exchange.
In refrigeration systems, our tubes are used in both domestic and commercial applications to transport refrigerant between different components, ensuring efficient cooling and preserving food and other items. Their ability to withstand high pressures and resist corrosion ensures reliable and long-lasting performance.
For heating systems, such as boilers and heat pumps, our copper tubes are designed to optimize heat transfer and energy efficiency, providing warmth in residential, commercial, and industrial spaces.
Our brass rods are extensively used in HVAC&R systems for their excellent machinability, corrosion resistance, and durability. They are commonly used to manufacture fittings, valves, and connectors that are essential for the assembly of HVAC&R equipment. Their function is to create leak-proof joints and to control the flow of refrigerant or other heating fluids, ensuring efficient operation and easy maintenance.
Overall, our comprehensive range of extruded copper and copper alloy products enhances the functionality and reliability of complex systems, supporting seamless integration and superior performance across the HVAC&R industry.
Products per sector
Select your desired sector
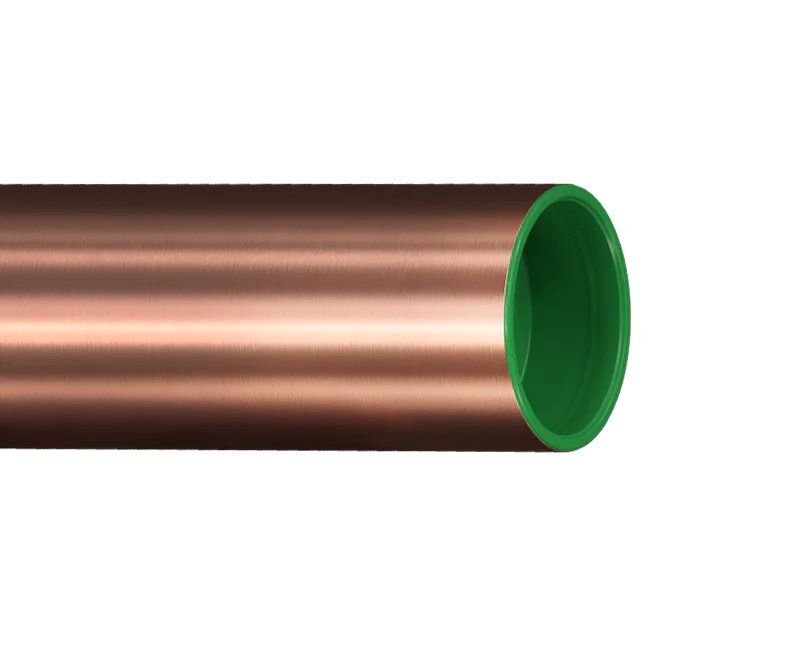
TALOS® XS
Refrigeration systems, Fittings
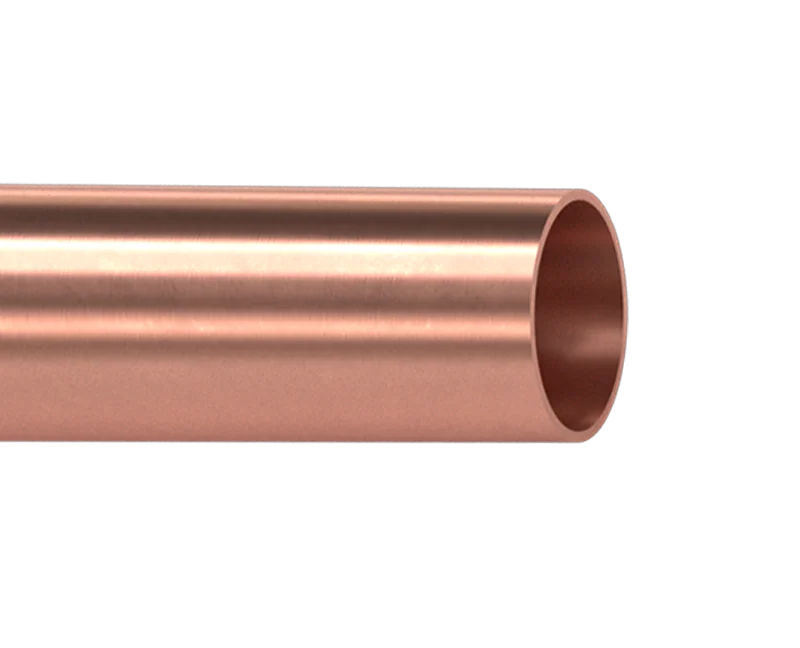
TALOS® S80
Refrigeration systems
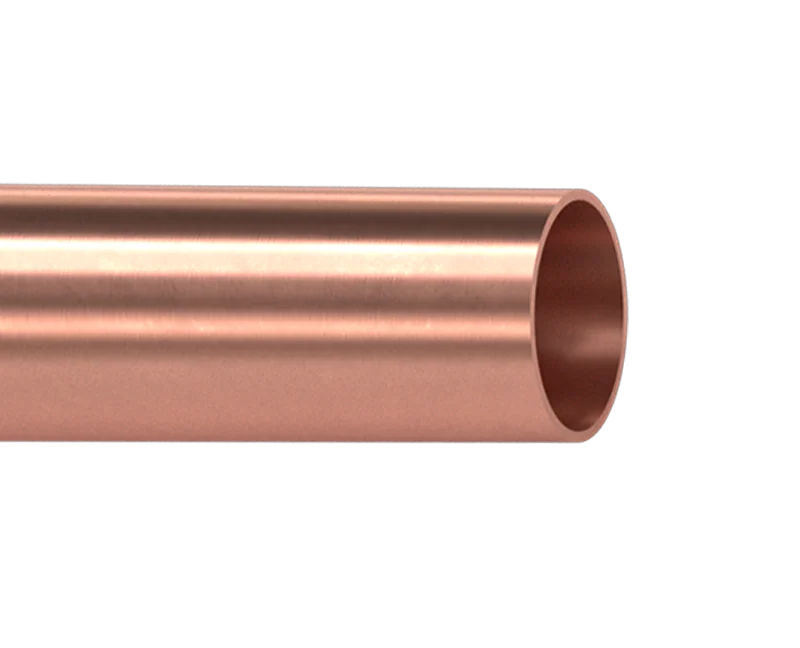
TALOS® S60
Refrigeration systems
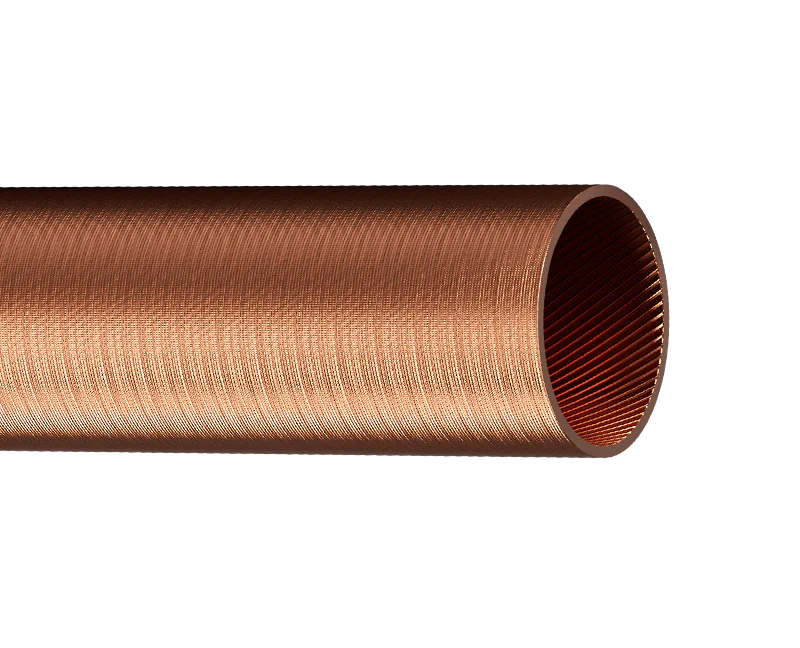
TALOS® FIN
Refrigeration systems, Heating systems, Air-conditioning systems, Heat exchangers

TALOS® ACR ECUTHERM II™
Air-conditioning systems, Refrigeration systems
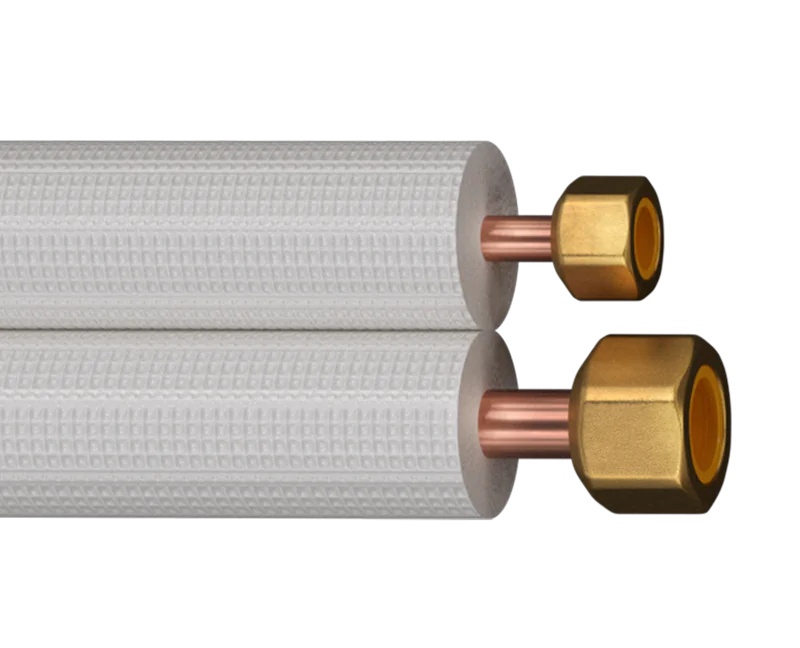
TALOS® ACR LINESETS
Heat pumps, Air-conditioning systems
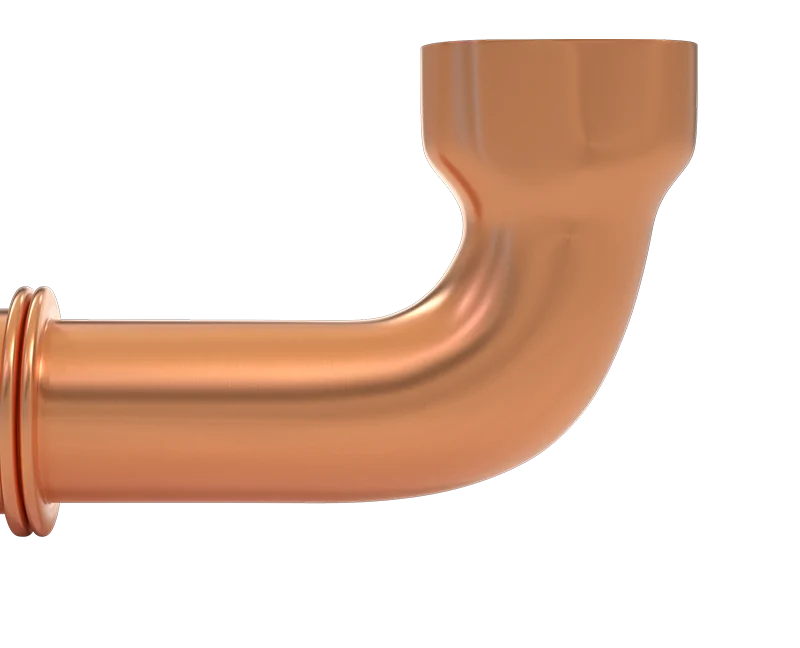
TALOS® FORM
Fabricated parts, Filters, Connection fittings, Accessories
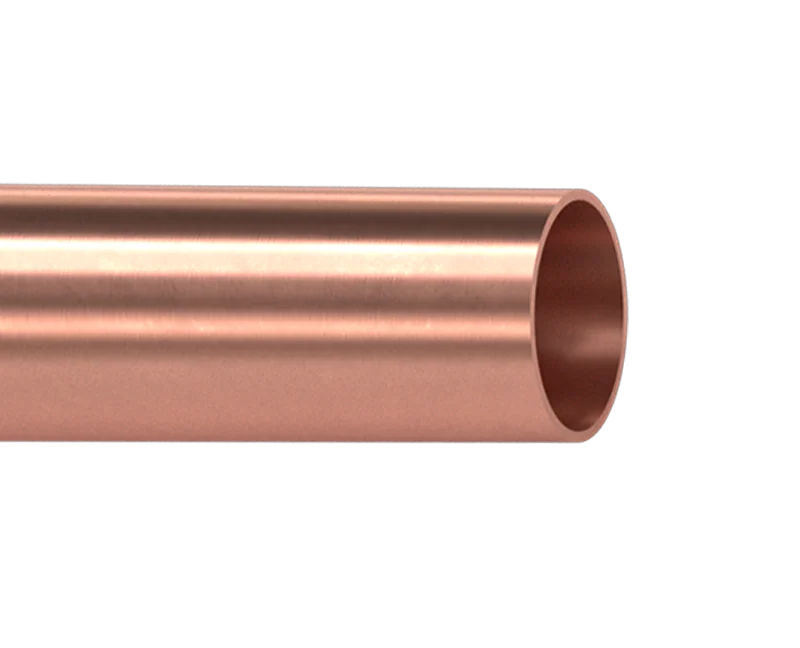
TALOS® ACR
Refrigeration systems, Air-conditioning systems, Heat pumps
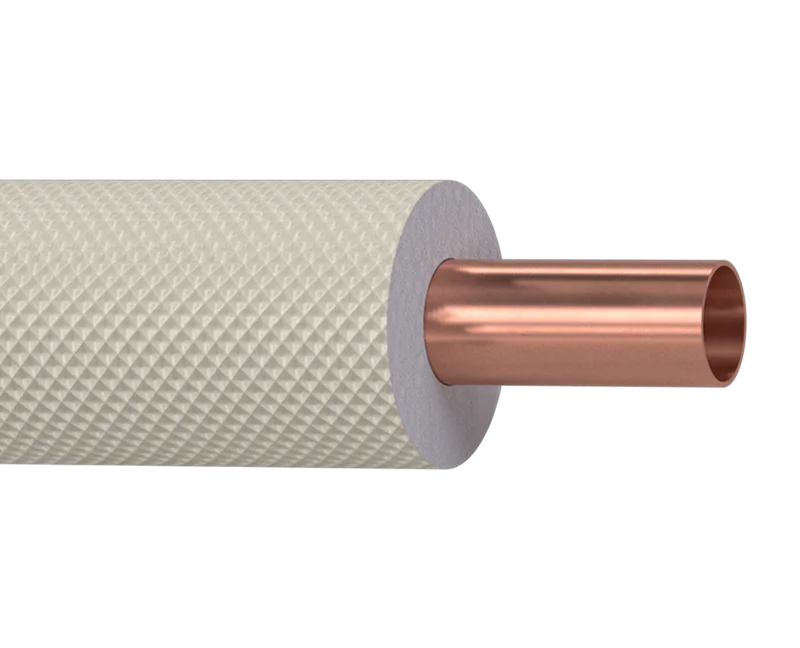
TALOS® ACR ECUTHERM™
Refrigeration systems, Air-conditioning systems, Heat pumps
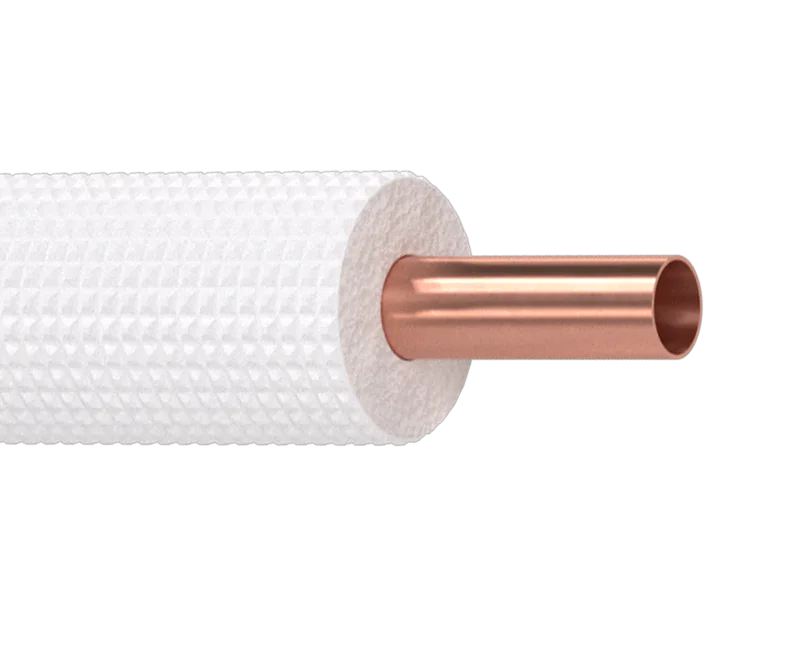
TALOS® ECUTHERM™
Water Supply, Heating, Solar Systems
04-10-2022
Evolving beyond copper: The storyline behind HALCOR’s new tagline.
For the past 85 years, HALCOR has been synonymous with copper, internationally. For the company, copper is not simply a raw material; it is the driving force that makes it move forward; that has brought it to the point where it is today and has established it as one of the leading producers of copper & copper alloys in Europe.
Today Halcor is continuing to evolve and is accelerating its growth.
That’s how its new tagline, “Evolving beyond copper” came up. A key message aimed at both the Greek and global market, which suggests that HALCOR evolves copper, brass, and other copper alloys, while at the same time it evolves as an organization as well.
What does “Evolving beyond copper” mean
The notion of the evolution of copper does not refer merely to the new, pioneering alloys of the company. It’s about something bigger and wider than the features of its products; it’s about its vision and tomorrow’s HALCOR.
“Evolving beyond copper” is about a company that invests in ultramodern production units, increasing its yield, and thus holding the leading position in the production of copper tubes in EMEA. That is utilizing high-tech infrastructures created after significant investment, such as the tube heat transfer laboratory, to develop solutions adapted to the needs of its customers. That is becoming, though its advanced offering, a valuable ally to its customers, building long-term relationships that ensure its future growth.
“Evolving beyond copper” is about a company that looks ahead; creates the products of tomorrow; invests in research; invents innovative solutions; supports international sectors, such as HVAC, allowing them to further develop.
“Evolving beyond copper” is about a company that introduces new services in the industrial world; stands out for its unbeatable after-sales service; is recognized as a one-stop-shop that offers the widest range of sharply specialized services; relies on its own strength and is thus able to handle any requirement by any customer.
And, of course, “Evolving beyond copper” is about a responsible company, that is acting towards a sustainable future for all.
All this – and even more – is the meaning of HALCOR’s new message, today. And it will undoubtedly encapsulate more meanings in the future. Because HALCOR is one, forward-looking, ceaselessly evolving team. A team now equipped with the tagline that reflects its creative restlessness and its need to constantly become better.
Follow Halcor on LinkedIn.
20-06-2021
Halcor receives award for copper and copper alloys recycling at the “Bravo Sustainability Dialogue & Awards 2020”
Press Release
Athens, 07/06/2021
Halcor, the copper tubes division of ElvalHalcor, was awarded for its approach in the recycling of copper and copper alloys, in the scope of the “Bravo Sustainability Dialogue & Awards,” which took place in an online event, on Friday, June 4, 2021.
Participating at this event, with a short greeting, Mr. Nikos Marinakis, Director of Halcor’s Foundry Plant, stated that: “We invest steadily in sustainability and the implementation of responsible practices. We place a special emphasis on recycling and have implemented an extensive program to use recycled copper or aluminum as a raw material. For Halcor, ElvalHalcor’s copper tubes division, in 2020 the needs for raw materials were covered at a rate of 55% by secondary sources, i.e. by copper scrap, sourced from a collection of products after the end of their life cycle. We strategically seek the ever-increasing integration of copper scrap as a raw material for the production of our products, thus contributing to the circular economy, with the aim of saving natural resources and reducing our environmental footprint”.
About Halcor
Halcor is the copper tubes division of ElvalHalcor S.A., a leading copper industry that specializes in the production, processing and marketing of copper and copper alloys products with dynamic commercial presence in the European and global markets. For more than 80 years, Halcor has been offering innovative and added value solutions that meet contemporary client demands in fields, such as plumbing, HVAC&R, renewable energy, architecture, engineering and industrial production.
About the “Bravo” Initiative
Bravo is a nationally developed sustainable development dialogue forum which is based on initiatives implemented by Greek Businesses, Local Government Organizations and Civil Society. Bravo’s 250 Initiatives and the 35,000 active citizens participating with it have led to the wider sharing of information and a broader awareness within Greek society as well as an exchange network for knowledge and experience from these organizations, contributing to the creation of the “Greece of Tomorrow” initiative. Bravo dialogue and awards.
bravosustainabilityawards.com
02-11-2020
Elval is the first Greek manufacturer to certify its casthouse, rolling, coil coating and finishing operations to the Aluminium Stewardship Initiative (ASI) Performance Standard
Athens, 22 October 2020
Elval, aluminium rolling division of ElvalHalcor announces the certification of its production facilities at Oinofyta, Greece to the ASI Performance Standard. The certification audit was conducted by DNV GL and it covered all the policies, procedures, infrastructure and practices that are in place against the criteria of the standard.
Mr. Lampros Varouchas, Managing Director of Elval stated: “We are proud to develop industry-leading aluminium solutions, fully embracing the principles of sustainable growth, which has always been a core objective for Elval. The certification of our operations at Oinofyta plant to the ASI Performance Standard reinforces our profound commitment on responsible production and demonstrates the efficiency of our procedures and methods on environmental protection, social responsibility and corporate governance towards our employees, our business partners, our customers, the society and all our stakeholders”.
The ASI Certification program was developed through an extensive multi-stakeholder consultation process and is the only comprehensive voluntary sustainability standard initiative for the aluminium value chain. The ASI Performance Standard defines environmental, social and governance principles and criteria, with the aim to address sustainability issues in the aluminium value chain. It sets out 59 criteria under the three sustainability pillars of Governance, Environment and Social, which address key issues such as biodiversity, indigenous peoples rights, and greenhouse gas emissions.
As part of its sustainability programme, Elval shall subsequently pursue the certification to the ASI Chain of Custody standard and the supply of ASI material to its customers.
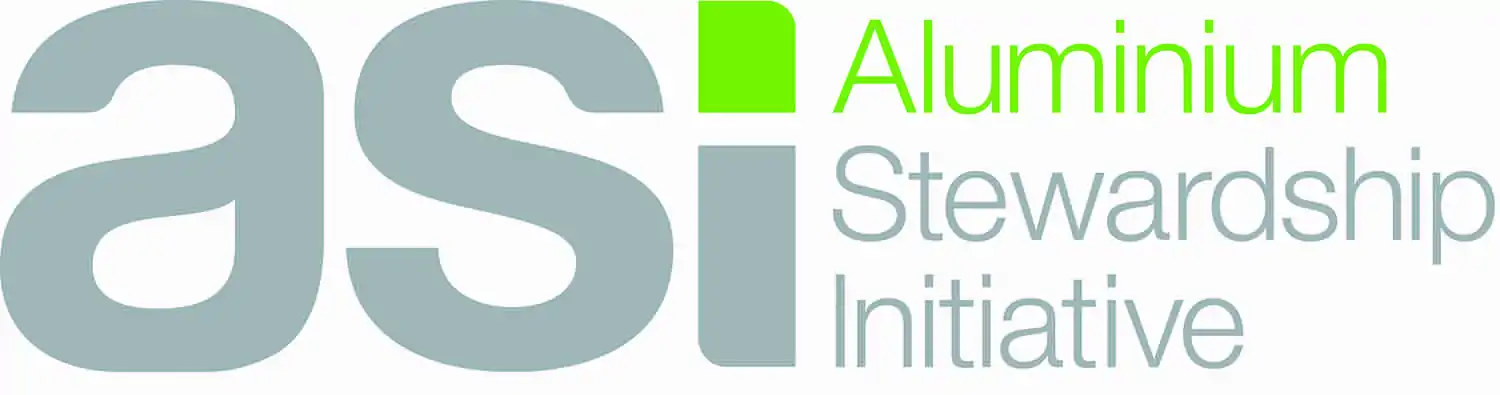
About ASI
The Aluminium Stewardship Initiative (ASI) is a global, multi-stakeholder, non-profit standards setting and certification organisation. It works towards responsible production, sourcing and stewardship of aluminium following an entire value chain approach. To this end, ASI launched its Performance Standard and Chain of Custody Standard in December 2017. For more info please visit the website: https://aluminium-stewardship.org
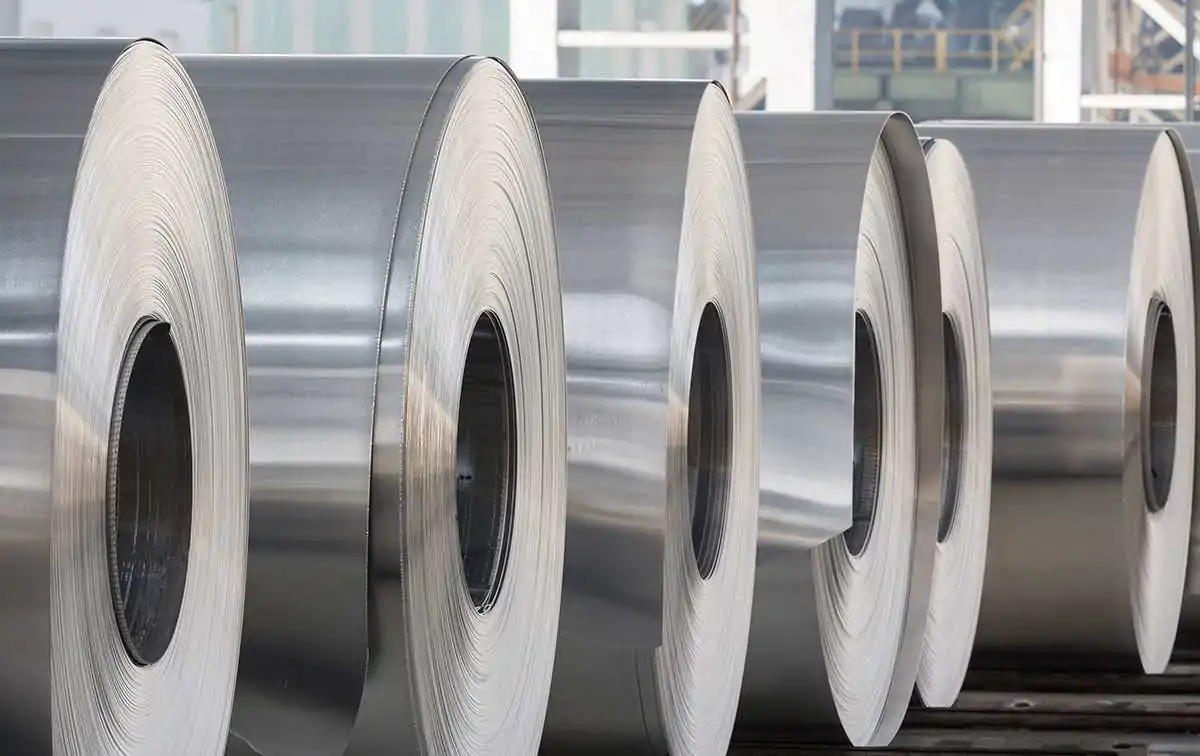
About Elval
Elval is the aluminium rolling division of ElvalHalcor S.A., one of the leading aluminium rolling manufacturers worldwide and the only one in Greece. For almost 50 years, Elval has been recognised as a trusted partner and innovative aluminium manufacturer, with a broad portfolio of quality products for the packaging, construction, shipbuilding, automotive, energy, industrial and HVAC markets. Through an established global commercial network across 21 countries, Elval exports approximately 80% of its production to more than 60 countries and offers reliable, sustainable and competitive solutions that meet the requirements of the most demanding global customers. For more information about Elval, please visit the website www.elval.com